Industry 4.0 has to cope with the necessity of producing within environmental constraints in order to meet the challenge of sustainability. On the one hand, it has been contended that new technologies (e.g., advanced robotics, internet of things, additive manufacturing) can produce an increase in resource efficiency, for instance by reducing errors and improving the precision of production operations, allowing for predictive maintenance and reducing manufacturing waste, in line with the circular economy paradigm. On the other hand, despite possibilities of energy optimisation provided by algorithms and data analytics, energy consumption represents a concrete challenge especially in relation to additive manufacturing; furthermore, the demands of raw materials and rare earth elements (e.g., lithium, dysprosium/terbium and rhenium) are expected to grow for the production of drones, sensors and other devices. Not to mention the increasing concerns for e-waste dumping in the Global South where no protocols or regulations exist.
To deal with this challenge, workers’ reps should deepen their knowledge about the environmental impact of Industry 4.0-related technologies and raise workers’ awareness of the role they can play in gearing modern production towards sustainability. Above all, a strong sustainability culture (overcoming
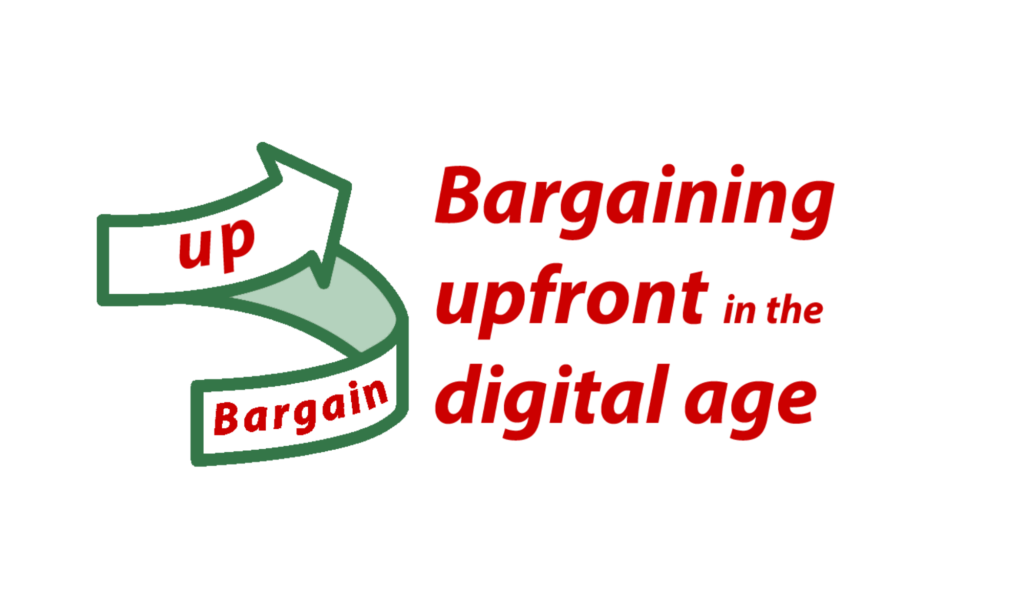
the presumed trade-off between work, production and the environment) must be created in workplaces and workers’ reps should tailor training activities towards this objective. More participatory rights at all levels of industrial relations are also needed to allow workers and their representatives to be informed in due time about development strategies and play a concrete role in converging Industry 4.0 and environmental sustainability. This may entail, for instance, the revision of school curricula and company training courses and the provision of occupational transition programmes assisting workers potentially affected by radical company restructuring. Trade unions must thus adopt a future-oriented perspective, entailing partnerships and alliances with civil society actors and other key public and private stakeholders to design and build green industries and economies.