Whereas the adoption of digital technologies is proceeding, while at differentiated paces in European countries despite the upsurge of remote working and learning after the outbreak of COVID-19 pandemic, there are several estimates and already some evidences on their impact on the world of work. On the one side, there are studies casting light on a considerable proportion of jobs threatened by digitalisation, a polarisation of competences in labour markets, whereby a growing share of highqualification activities is accompanied by persisting easy and non-automatable tasks, and the paradoxical combination of decentralisation and multifunctional roles with standardisation and control tasks in modern work-organisational models. On the other side, analyses emphasise the longterm employment creation resulting from digital technologies, an upgrading of qualifications and skills due to the increasing complexity of digitised industrial work, and self-organised and highly flexible work organisation systems. The picture is complex and after all, as the ETUC resolution (2016) pointed out, ‘nobody has a crystal ball to look into the digital future and there is no such thing as technological determinism related to digitalisation’. Further complicating the situation are the issues of climate change and the aging population, both requiring structural reforms in the economy and society.
To deal with this challenge, workers’ reps should build, along with other political and social players, the necessary infrastructural conditions to grasp the opportunities arising from digitalisation and environmental sustainability, while preventing the exacerbation of long-standing issues (e.g., wage and
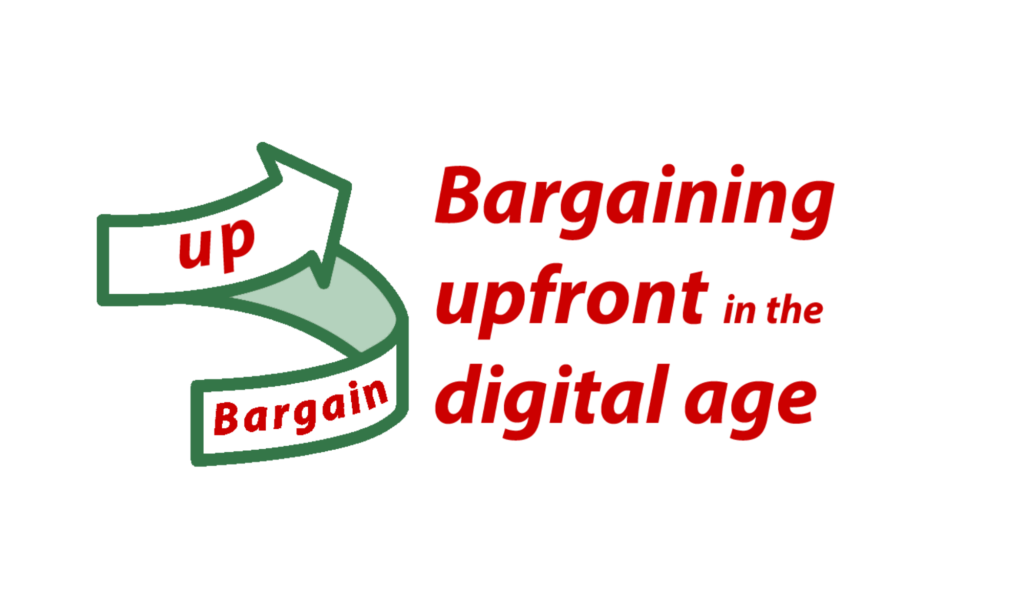
income inequality, poverty, unemployment, gender disparities, etc.) due to the pressure of new ones. They should adopt an anticipatory and proactive approach to transformations at national and cross-national, local and company level. Workers’ reps should thus engage with employers in phased innovation plans starting with joint analyses and assessments of existing situations, also in collaboration with external experts and institutes, to get in-depth information in due time; they should then prepare the ground for innovation by jointly delivering the skills needed to workers and managers; outline shared developmental plans with testing phases, priority setting, time-bound phases and support tools; and collectively monitor and evaluate the processes, thus implementing the necessary adjustments and follow-ups. Finally, workers’ reps should make sure that productivity paybacks are equally distributed among the workers enabling them.
Workers’ Training and Involvement to Accompany Technological Changes at Renault España
Collective Governance of Innovation and the Redistribution of Related Economic Results at Italian Company Rold
Enabling Workers’ Representatives to Bargain over Digitalisation: the Case of Arbeit 2020
Further information at https://www.arbeit2020.de.
The ‘House of the Worlds of Work’ Guiding the Future of Work at the Germany Pharmaceutical Company Merck
Further information at https://www.boeckler.de/pdf/mbf_bvd_portrait_haus_der_arbeitswelten.pdf.